The Scientific Research Behind Porosity: A Comprehensive Overview for Welders and Fabricators
Understanding the detailed systems behind porosity in welding is essential for welders and fabricators making every effort for flawless craftsmanship. From the make-up of the base materials to the intricacies of the welding procedure itself, a wide range of variables conspire to either exacerbate or relieve the existence of porosity.
Understanding Porosity in Welding
FIRST SENTENCE:
Assessment of porosity in welding discloses important understandings into the stability and top quality of the weld joint. Porosity, defined by the visibility of cavities or gaps within the weld steel, is a common worry in welding procedures. These voids, if not effectively resolved, can endanger the architectural honesty and mechanical residential properties of the weld, leading to potential failures in the completed item.

To find and quantify porosity, non-destructive testing methods such as ultrasonic screening or X-ray evaluation are typically utilized. These methods permit the recognition of interior problems without endangering the honesty of the weld. By evaluating the dimension, shape, and circulation of porosity within a weld, welders can make educated choices to boost their welding procedures and attain sounder weld joints.

Elements Influencing Porosity Development
The occurrence of porosity in welding is affected by a myriad of elements, varying from gas protecting performance to the intricacies of welding specification setups. Welding parameters, consisting of voltage, current, travel rate, and electrode type, additionally impact porosity formation. The welding method employed, such as gas steel arc welding (GMAW) or shielded metal arc welding (SMAW), can affect porosity formation due to variants in warm circulation and gas coverage - What is Porosity.
Impacts of Porosity on Weld Top Quality
Porosity formation substantially endangers the structural integrity and mechanical buildings of welded joints. When porosity exists in a weld, it produces gaps or cavities within the material, minimizing the total stamina of the joint. These voids serve as anxiety focus points, making the weld much more vulnerable to fracturing and failing under lots. The visibility of porosity also compromises the weld's resistance to rust, as the caught air or gases within deep spaces can respond with the surrounding setting, bring about degradation over time. Additionally, porosity can impede the weld's capability to withstand pressure or impact, further endangering the overall high quality and reliability of the bonded framework. In essential applications such as aerospace, automotive, or architectural building and constructions, where safety and security and resilience are paramount, the detrimental effects of porosity on weld quality can have extreme effects, stressing the value of lessening porosity through proper welding strategies and procedures.
Strategies to Minimize Porosity
Additionally, using the proper welding specifications, such as the proper voltage, present, and take a trip rate, is crucial in avoiding porosity. Preserving a regular arc size and angle during welding visit site also assists minimize the probability of porosity.

In addition, choosing the best protecting gas and preserving correct gas circulation prices are crucial in minimizing porosity. Making use of the proper welding strategy, such as back-stepping or using a weaving movement, can likewise assist disperse warmth uniformly and reduce the chances of porosity formation. Guaranteeing proper ventilation in the welding environment to eliminate any type of prospective sources of contamination is crucial for accomplishing porosity-free welds. By executing these strategies, welders can successfully decrease porosity and create premium welded joints.
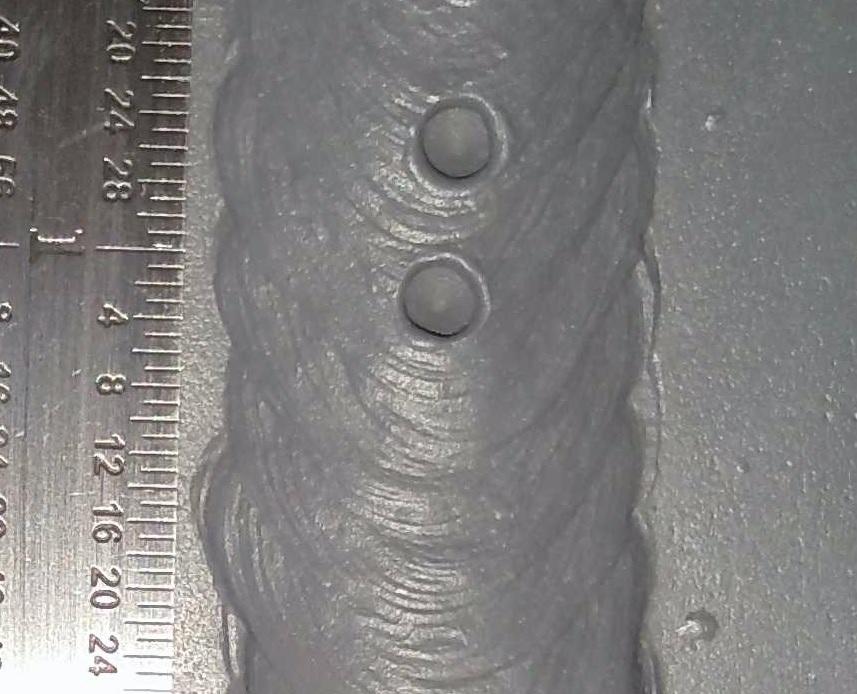
Advanced Solutions for Porosity Control
Carrying out advanced technologies and ingenious approaches plays an essential role in accomplishing remarkable control over porosity in welding procedures. One sophisticated remedy is making use of advanced gas combinations. Protecting gases like helium or a mix of argon and hydrogen can assist decrease porosity by providing far better arc stability and boosted gas coverage. In addition, employing advanced welding methods such as pulsed MIG welding or modified ambience welding can also assist mitigate porosity problems.
An you could look here additional innovative solution includes using innovative welding tools. Using equipment with built-in features like waveform control and sophisticated power sources can boost weld top quality and reduce porosity risks. In addition, the application of automated welding systems with accurate control over criteria can significantly minimize porosity issues.
Furthermore, integrating advanced monitoring and inspection technologies such as real-time X-ray imaging or automated ultrasonic screening can help in discovering porosity early in the welding process, permitting immediate rehabilitative activities. Generally, incorporating these sophisticated solutions can greatly improve porosity control and boost the total high quality of welded click here to find out more parts.
Verdict
To conclude, comprehending the science behind porosity in welding is crucial for welders and makers to create high-grade welds. By recognizing the elements influencing porosity formation and implementing strategies to lessen it, welders can improve the total weld quality. Advanced options for porosity control can additionally enhance the welding procedure and ensure a solid and trustworthy weld. It is necessary for welders to continually inform themselves on porosity and implement best methods to achieve ideal outcomes.